In the world of prototyping, medical simulations, and creative design, the choice between 3D printed and silicone models can be pivotal. Both technologies offer unique advantages, but understanding the differences and applications of each is crucial to making an informed decision. In this blog post, we will compare 3D printed and silicone models to help you determine the better fit for your project.
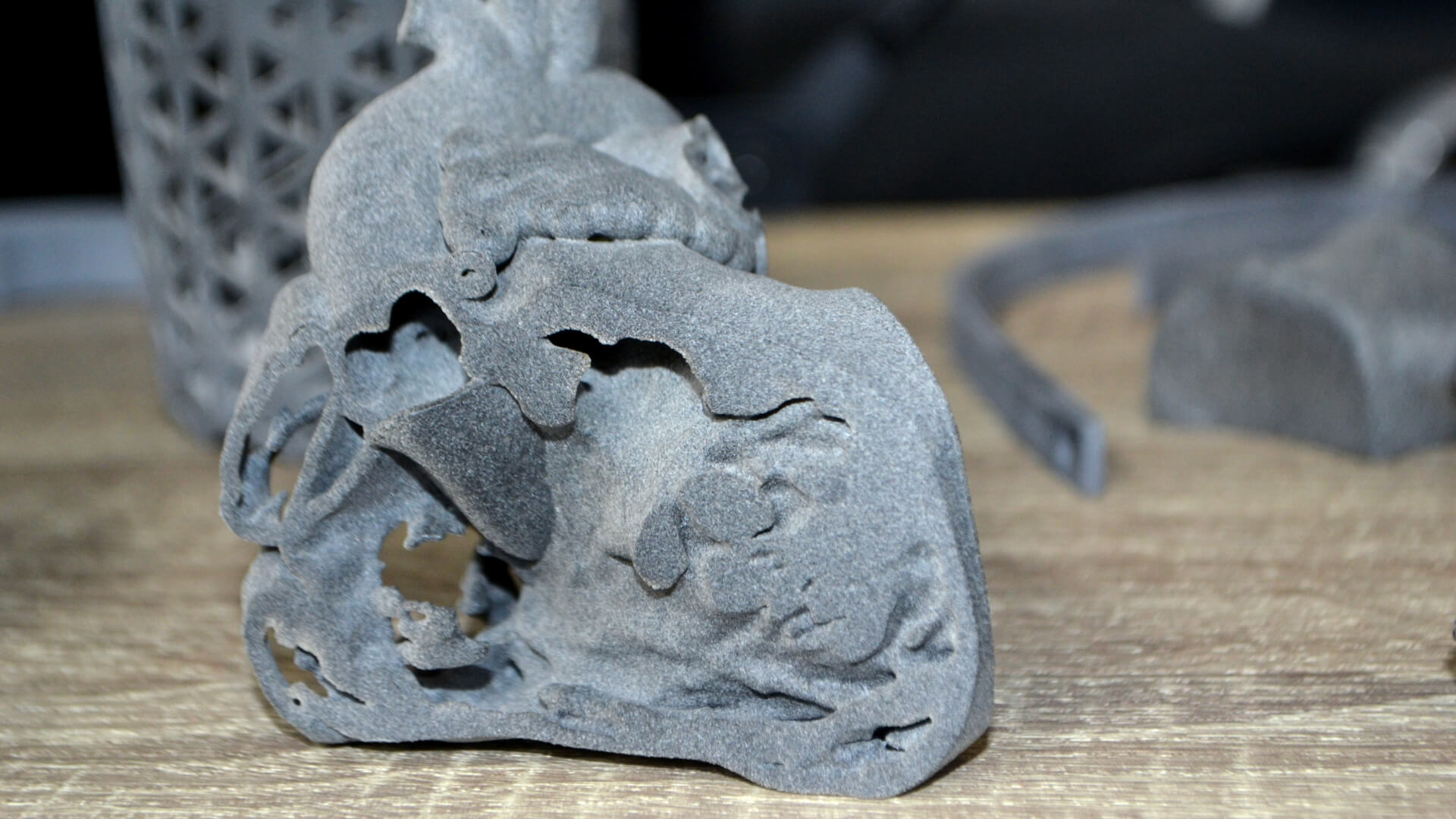
Material Properties
3D Printed Models:
3D printing involves layering material, typically plastic or resin, to build the desired shape.
The material properties can vary widely, with options like PLA (Polylactic Acid), ABS (Acrylonitrile Butadiene Styrene), or specialised resins.
Depending on the material chosen, 3D-printed models can have varying levels of strength, flexibility, and durability.
Silicone Models:
Silicone is known for its flexibility, elasticity, and soft-touch feel, making it ideal for certain applications like medical simulations or soft robotics.
Silicone can be colour-tinted or mixed with additives for specific characteristics such as translucency or hardness.
Accuracy and Precision
3D Printed Models:
3D printing offers high precision and accuracy, especially when using advanced printers with fine resolution.
It is excellent for creating intricate and complex geometric shapes with fine details.
Tolerance levels can be controlled to produce parts with minimal deviation from the design specifications.
Silicone Models:
Silicone casting can achieve high detail and precision, but it may require meticulous manufacturing techniques.
It excels in replicating organic shapes and textures, such as human body parts or natural forms.
The flexibility of silicone can mimic the feel of real tissue or skin in medical simulations.
Cost and Speed
3D Printed Models:
3D printing is often more cost-effective for small-batch production or prototyping, as it reduces the need for expensive moulds.
It can be a faster process for producing prototypes or one-off designs, especially with rapid prototyping techniques.
Silicone Models:
Creating silicone models can be expensive and time-consuming, particularly for intricate designs.
However, for large-scale production runs, silicone can be more cost-effective in the long run, as it allows for consistent replication.
Applications
3D Printed Models:
3D printing is widely used across various industries, including aerospace, automotive, architecture, and consumer goods.
It is excellent for creating prototypes, functional parts, and complex mechanical components.
Silicone Models:
Silicone models find applications in medical training and simulation, special effects in film and TV, prosthetics, and soft robotics.
Its unique tactile properties make it valuable for replicating human tissue, organs, or special effects makeup.
Choosing between 3D printed and silicone models ultimately depends on your specific project requirements. Consider factors such as material properties, accuracy, cost, and application when making your decision.
If you need precise, geometrically complex parts quickly and at a lower cost, 3D printing may be your best choice. On the other hand, if your project requires soft, flexible, and tactile models, silicone casting is likely the better option. Ultimately, understanding the strengths and weaknesses of each technology will help you make an informed decision to bring your project to life.